有困扰时?
目录
1. 开始
如果滚动轴承的选择、环境、安装和维护不恰当,则会出现损伤。
在确定滚动轴承损伤原因时,原因往往是多种多样的,而且很难推测真正的原因。 这里列出了滚动轴承损伤情况,并列出了主要原因和对策实例。希望能对您有所帮助。
但是,如果在充分了解使用条件后调查损伤情况,也可以确定原因。
参考规格 JIS B 1562:2009 滚动轴承-损伤及故障-用语、特性及原因
2. 滚动轴承损伤形式的分类
将滚动轴承的损伤原因分为7种。如图1所示。
第3至3.7节列举了损伤事例、原因和对策。
此外,附录1损伤分析表也有记载。
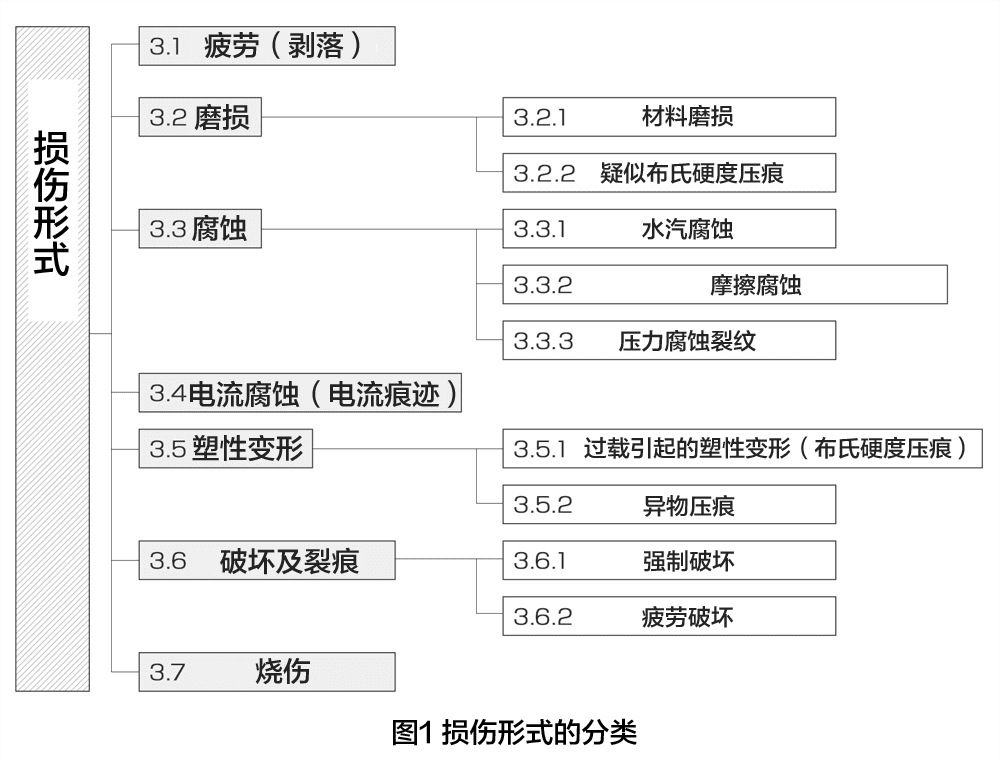
3 损伤形式
3.1 疲劳(剥落)(微裂纹;剥落或纵摇)
疲劳是由滚动元件和轨道之间的接触产生的循环应力引起的材料结构的变化。 疲劳表现为表面的微小剥落(剥落或倾斜)。
现象 | 当轴承在负载下旋转时,内圈和外圈滚道表面或球的滚动表面因滚动疲劳而脱落的现象 |
---|---|
原因 |
|
对策 |
|
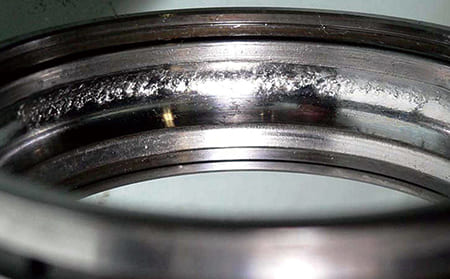
- 现象
- 发生在轨道平面末端的圆周上
- 原因
- 過过载、预压过大、安装不良(错位)
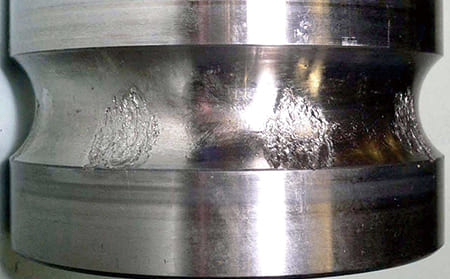
- 现象
- 轨道表面的末端出现球间距
- 原因
- 安装时的冲击载荷或是安装不良(错位)产生的压痕

- 现象
- 球间距发生在轨道的中心
- 原因
- 由于内部冷凝或水分渗入而生锈
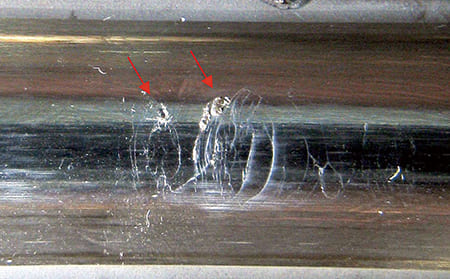
- 现象
- 在轨道中心的球行程轨迹中发生微裂纹(剥落或纵摇)
- 原因
- 初期阶段的材料滚动疲劳
3.2 磨损
磨损是通过两个滑动接触表面的相互作用或滚动/滑动接触表面的凹凸的相互作用,材料逐渐磨损的现象。
3.2.1 材料磨损
现象 | 随着滚动接触表面和保持器的磨损,表面逐渐变钝,最终发生加速磨损现象。 |
---|---|
原因 |
|
对策 |
|
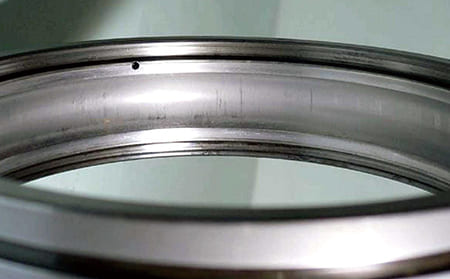
- 现象
- 滚动面整体钝化,发生磨损
- 原因
- 侵入轴承内部的粉尘
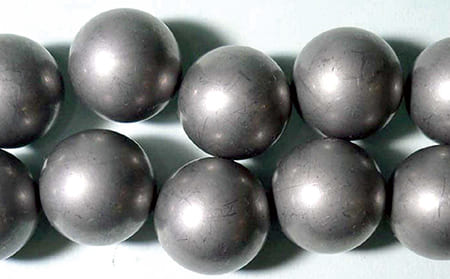
照片2-1的球
- 现象
- 球的整体表面钝化,发生磨损
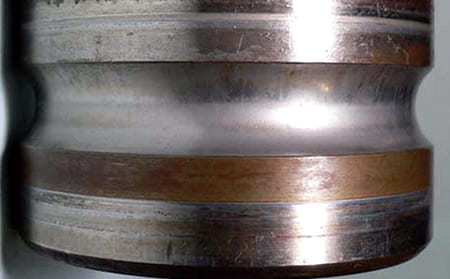
- 现象
- 沟道面的边缘发生圆周性的无光泽
- 原因
- 安装不良(安装误差)导致的润滑不良
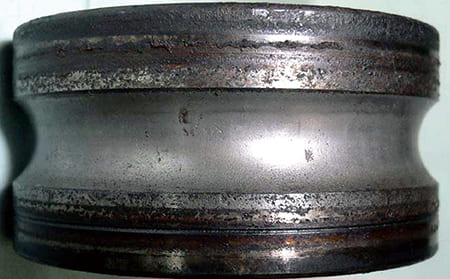
- 现象
- 沟道面整体无光泽(粗糙),发生磨损
- 原因
- 轴承内部进入污泥
3.2.2 疑似布氏压痕(微震腐蚀)
现象 | 周期性的震动下,微小运动导致钢球与沟道的接触面形成凹坑,产生腐蚀与磨损 |
---|---|
原因 |
|
对策 |
|
备注 ・・・疑似布氏压痕,被分类为腐蚀
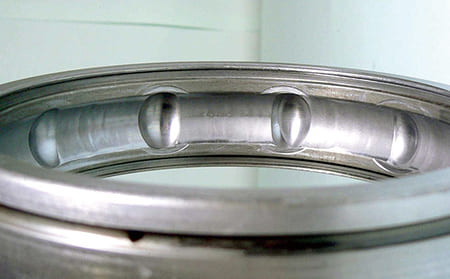
- 现象
- 钢球间距中局部发生凹陷磨损
- 原因
- 小幅度摇动运动导致润滑不良
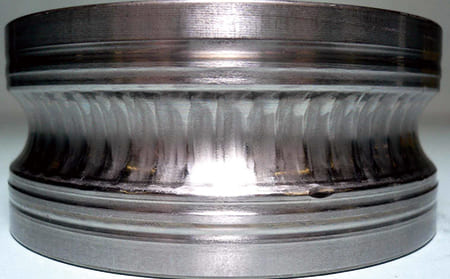
- 现象
- 沟道的钢球运行轨迹发生鳞状磨损
- 原因
- 低速运转时的周期性震动作用导致润滑不良
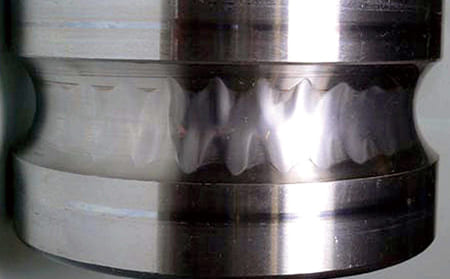
- 现象
- 沟道面上钢球的运行轨迹为蛇形,发生鳞状磨损
- 原因
- 低速运转时的周期性震动作用导致润滑不良
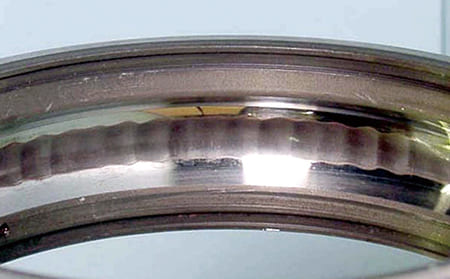
- 现象
- 沟道面的钢球运行轨迹变为茶色,发生鳞状磨损
- 原因
- 高速运转时的周期性震动作用导致润滑不良
3.3 腐蚀
腐蚀是指,金属材料与周围环境(相邻的金属、气体等)的物质发生化学反应,熔化或产生腐蚀生成物(生锈)的现象。
3.3.1 水汽腐食
现象 | 润滑脂或空气中的水分与轴承零件反应而产生的表面氧化现象 |
---|---|
原因 |
|
对策 |
|
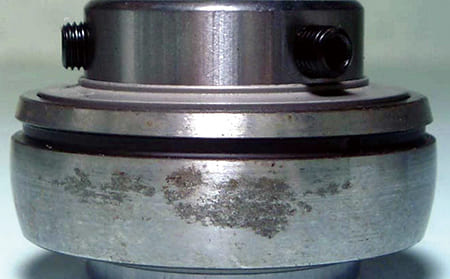
- 现象
- 轴承外径面发生氧化(锈)
- 原因
- 包装容器内部结露以及保存状态不适合
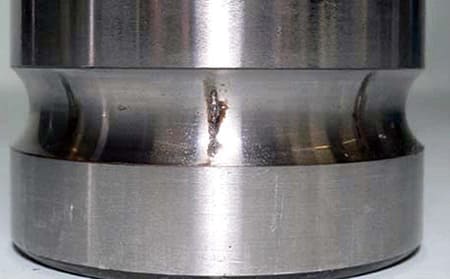
- 现象
- 沟道面的钢球间隔生锈
- 原因
- 轴承内部结露以及保存状态不适合
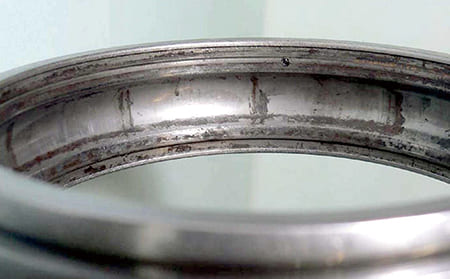
- 现象
- 沟道面无光泽(磨损),运转停止时钢球间隔生锈
- 原因
- 轴承内部水分侵入造成润滑不良
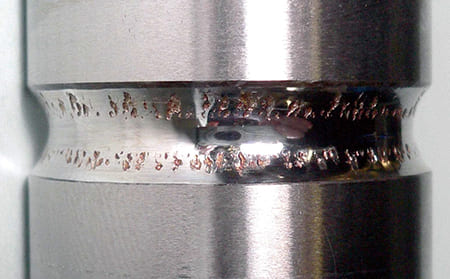
- 现象
- 虽可维持沟道光泽度,但发生异常磨损,造成沟道边缘局部腐蚀
- 原因
- 轴承内部水分浸入(溶剂)导致润滑不良
3.3.2 摩擦腐蚀 (微震侵蚀)(微震生锈)
现象 | 两个接触面(配合面)间相对的频繁的微小打滑而产生的磨损现象 |
---|---|
原因 |
|
对策 |
|
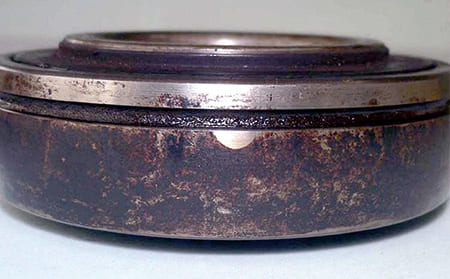
- 现象
- 轴承外径面氧化(锈蚀)发生磨损
- 原因
- 过大的荷重、震动的作用
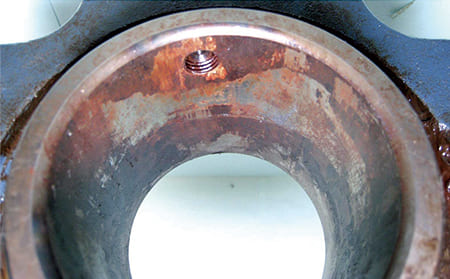
- 现象
- 轴承内径面发生一圈氧化(锈)
- 原因
- 锁紧不足、过大荷重、过大震动的作用
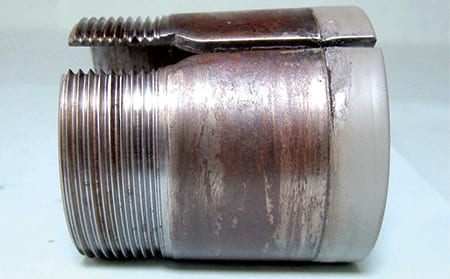
- 现象
- 紧固件外面的配合面氧化(生锈)发生磨损
- 原因
- 锁紧不充分、负荷过大、振动过大造成的
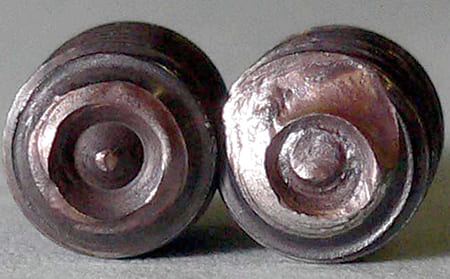
- 现象
- 止动顶丝顶端氧化(生锈)发生磨损
- 原因
- 顶丝锁紧不足,振动过大造成的
3.3.3 应力腐蚀断裂
现象 | 不锈钢这种材料在拉伸应力与腐蚀环境的相互作用下,材料上会出现裂纹,随着时间的推移逐步发展的现象 |
---|---|
原因 |
|
对策 |
|
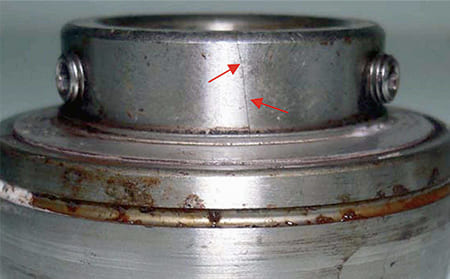
- 现象
- 不锈钢轴承两个止动顶丝之间产生裂纹
- 原因
- 含氯清洗剂的作用与顶丝锁紧时力量过大
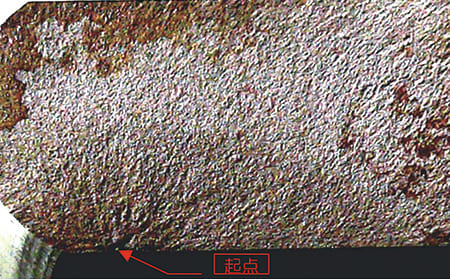
图片6-1的内圈宏观断面
- 现象
- 从顶丝侧内圈内径开始裂纹逐渐发展
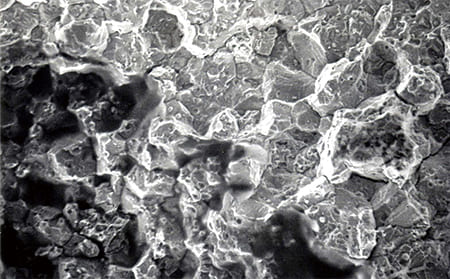
图片6-1的内圈微观断面
- 现象
- 金属结晶颗粒分离产生的断面(粒界断裂)
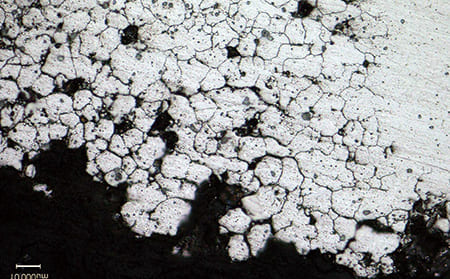
图片6-1的内圈微观组织
- 现象
- 内径面局部腐蚀,沿着粒界裂纹逐渐发展
3.4 电蚀(电解腐蚀)
电蚀是指由于导电产生的接触面材料脱落。
现象 | 由于电流通过轴承的润滑脂油膜,使钢球与轨道面的接触表面产生火花,并且接触区域相互熔化。 |
---|---|
原因 |
|
对策 |
|
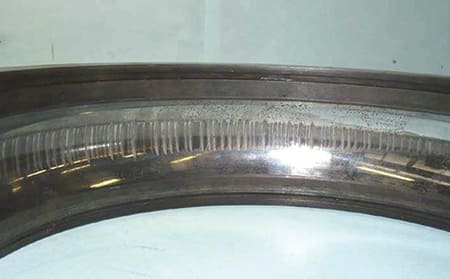
- 现象
- 外圈轨道面产生等距离的电解腐蚀(条状)烧伤
- 原因
- 由于绝缘不充分,在钢球与轨道面的接触区域产生火花
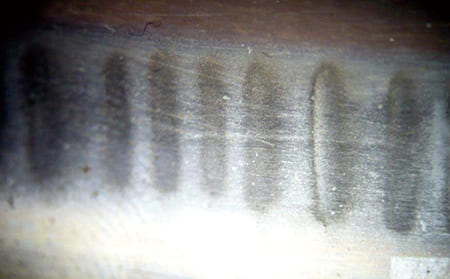
图片7-1の拡大
- 现象
- 与钢球的接触面材料脱落(凹坑)、凹坑部分变黑
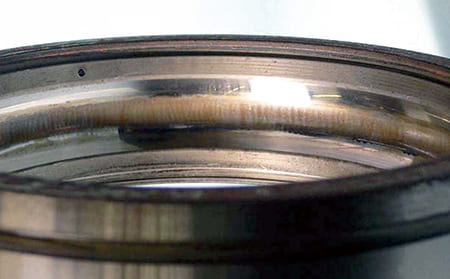
- 现象
- 外圈轨道面上电解腐蚀(条状)产生的浅烧伤
- 原因
- 在漏电强度比较弱的状态下钢球与轨道面的接触区域产生火花
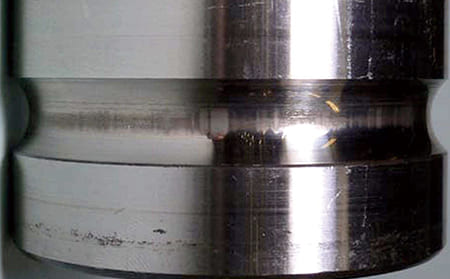
图片7-3的内圈
- 现象
- 内圈轨道面电解腐蚀(条状)产生的浅烧伤、变成浅黑色。
3.5 塑性变形
塑性变形是指物体在外力作用下产生的变形中,除去外力后不能恢复原状 的永久变形。永久变形会超过材料的弹性极限,有两种典型的表现。
- 宏观的:由于转动体与轨道间的接触负荷,在接触区域产生的大范围的降伏
- 微观的:由于转动体与轨道间夹杂(辗压)异物,只产生小范围的降伏
3.5.1 负荷过大造成的塑性变形(硬度压痕)
现象 | 静止的轴承受到静的或者冲击的过大负荷时,轨道面上产生球距间隔的浅坑或者沟的现象。 |
---|---|
原因 |
|
对策 |
|
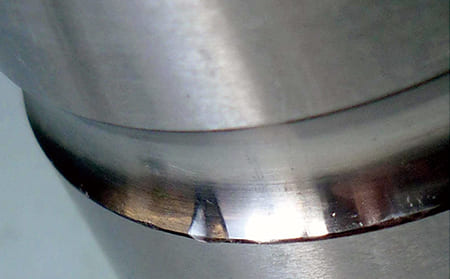
- 现象
- 单侧内圈轨道面球距间隔产生由钢球造成的压痕(凹坑)
- 原因
- 组装不合格或者施压过大
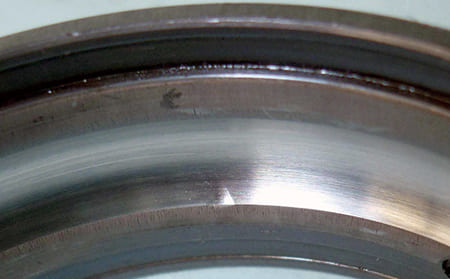
图片8-1的外圈
- 现象
- 单侧外圈轨道面球距间隔产生由钢球造成的压痕(凹坑)

- 现象
- 内圈轨道面中部产生由钢球造成的压痕(凹坑)
- 原因
- 负荷过大或者冲击负荷
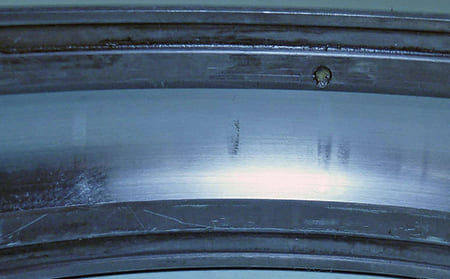
图片8-3的外圈
- 现象
- 外圈轨道面中间出现了钢球造成的凹痕
3.5.2 由异物造成的凹痕
现象 | 轨道面与钢球之间因有异物挤压造成了微小的凹陷 |
---|---|
原因 |
|
对策 |
|
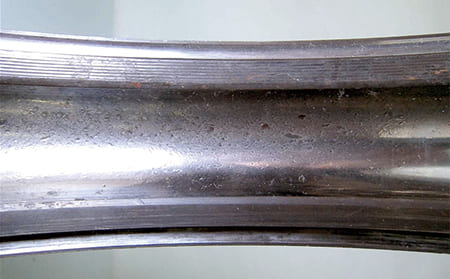
- 现象
- 轨道面的钢球运动轨迹上出现多处凹凸不平
- 原因
- 粉尘、异物侵入
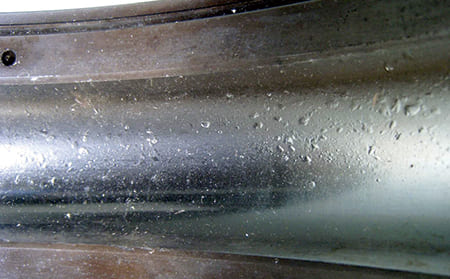
图片9-1放大
- 现象
- 轨道表面出现粉尘·异物的搅入和凹陷
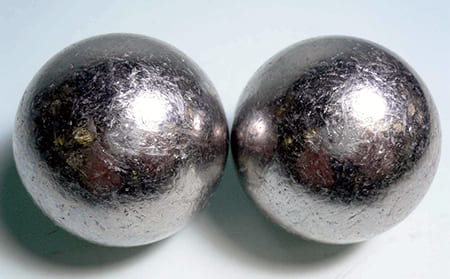
图片9-1的钢球
- 现象
- 钢球表面因搅入异物造成凹陷
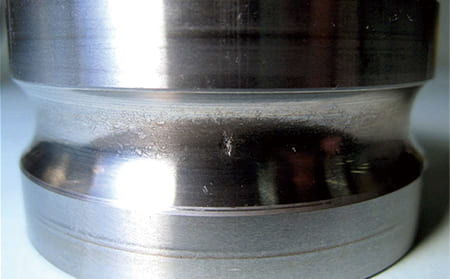
- 现象
- 轨道面外端的钢球行走轨迹出现多处细小的凹痕
- 原因
- 由轴承内部的滚动摩擦力增大,内部磨损产生的粉末搅入
3.6 损坏与裂纹
裂纹是材料在承受了超过其自身最大张力时会出现龟裂、甚至恶化蔓延。损坏是指裂纹蔓延后产品的一部分完全脱离解体的情况。
3.6.1 强制破坏
现象 | 由于冲击或紧固力度过大导致材料局部在承受了超出了 自身最大拉伸强度后出现损坏的现象 |
---|---|
原因 |
|
对策 |
|
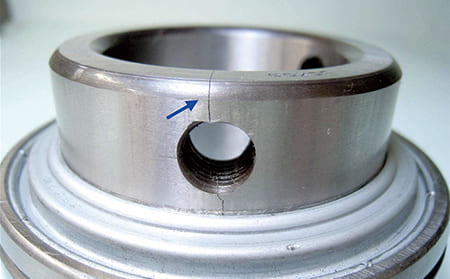
- 现象
- 由内圈螺孔向轴心方向产生龟裂
- 原因
- 紧固螺丝时用力过大
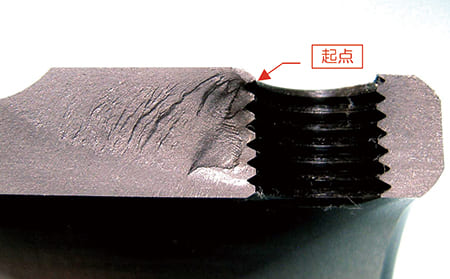
图片10-1的内圈断面
- 现象
- 断面的纹理是从螺孔的第一个螺丝牙向轴心方向延伸
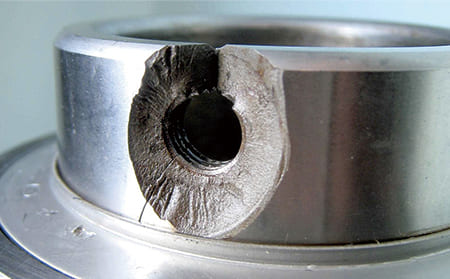
- 现象
- 从内圈的螺孔出现钵状龟裂,断面纹理由螺孔向外圈方向呈放射状蔓延
- 原因
- 紧固螺丝用力过猛
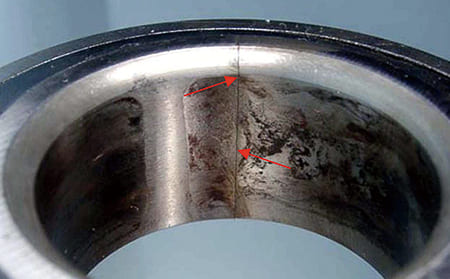
- 现象
- 带锁紧套轴承自内圈向轴心方向出现裂纹
- 原因
- 锁紧时用力过大
3.6.2 疲劳破坏
现象 | 在沟道轮、钢球及保持器上出现的弯折变形; 在拉伸或扭转情况时多次超过应力极限导致材料疲劳,出现裂纹 |
---|---|
原因 |
|
对策 |
|
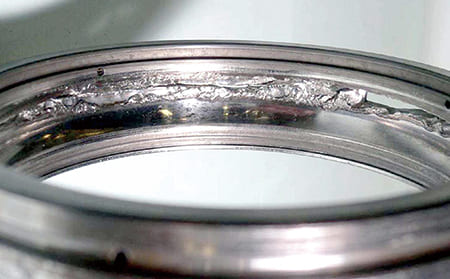
- 现象
- 外圈轨道面出现剥落,从轨道底部朝圆周方向破损
- 原因
- 外圈轨道的剥落现象加剧
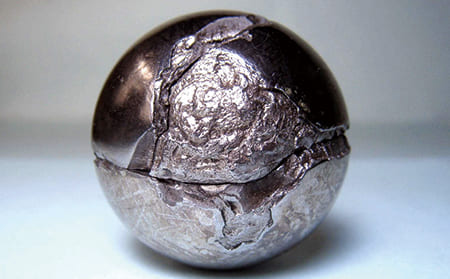
- 现象
- 钢球表面出现剥落,碎成两半
- 原因
- 钢球表面的剥落现象加剧
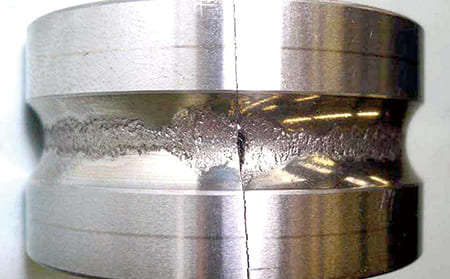
- 现象
- 带锁紧套轴承的内圈沟道面发生微震腐蚀,造成轴向损伤
- 原因
- 内圈沟道面发生微震腐蚀的发展
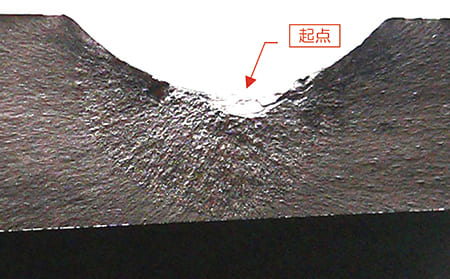
图片11-3中内圈损伤面
- 现象
- 内圈沟道面发生微震腐蚀的部分为中心,产生放射状的裂口
3.7 烧接
现象 | 运转中轴承发热,沟道轮、钢球以及保持器变色,软化,熔接,最后损伤轴承。 |
---|---|
原因 |
|
对策 |
|
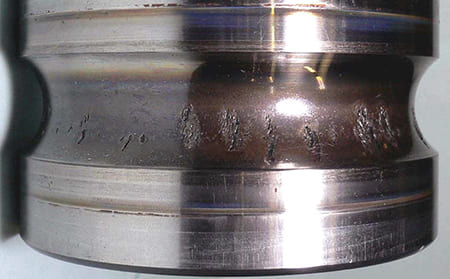
- 现象
- 内圈沟道面的钢球行迹变为褐色,发生微震腐蚀
- 原因
- 预压过大导致滚动摩擦增大
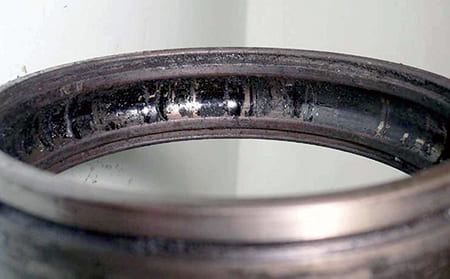
- 现象
- 外圈轨道面附着有黑色碳化的润滑脂
- 原因
- 受热导致润滑不良
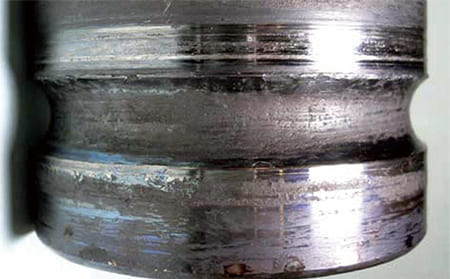
- 现象
- 内圈沟道面变为紫色,发生明显的粗糙部以及磨损
- 原因
- 轴承内部混入了粉尘导致润滑不良
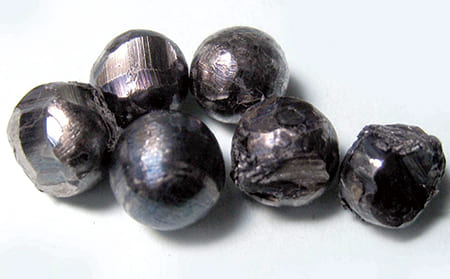
图片12-3的钢球
- 现象
- 钢球表面变为紫色,表面有摩擦导致损伤
表1 损伤分析表
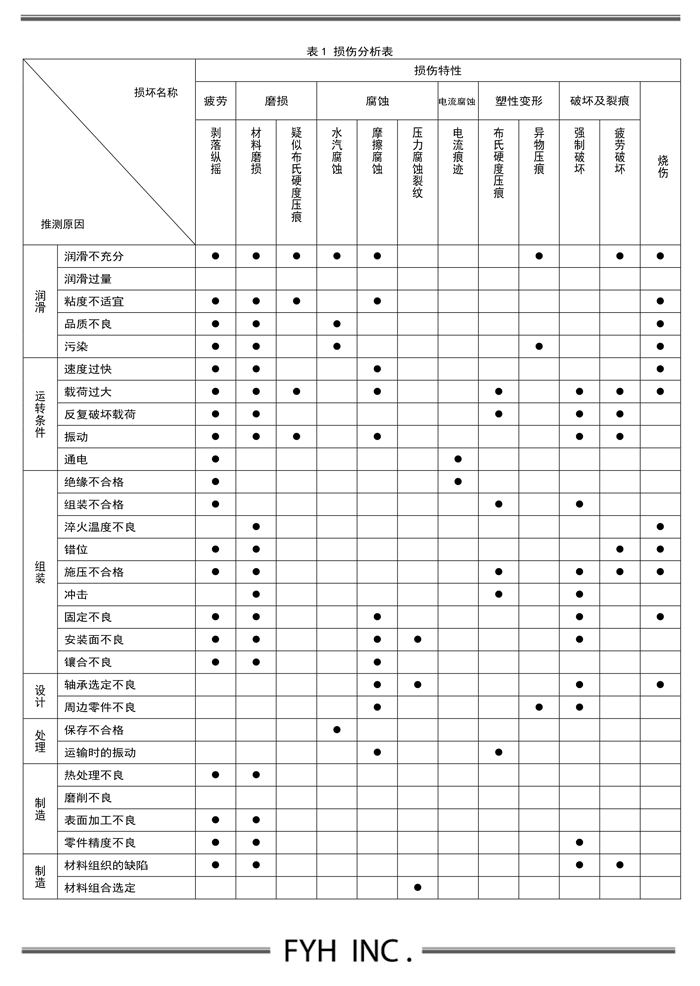
表1 损伤分析表表1 损伤分析表 PDF